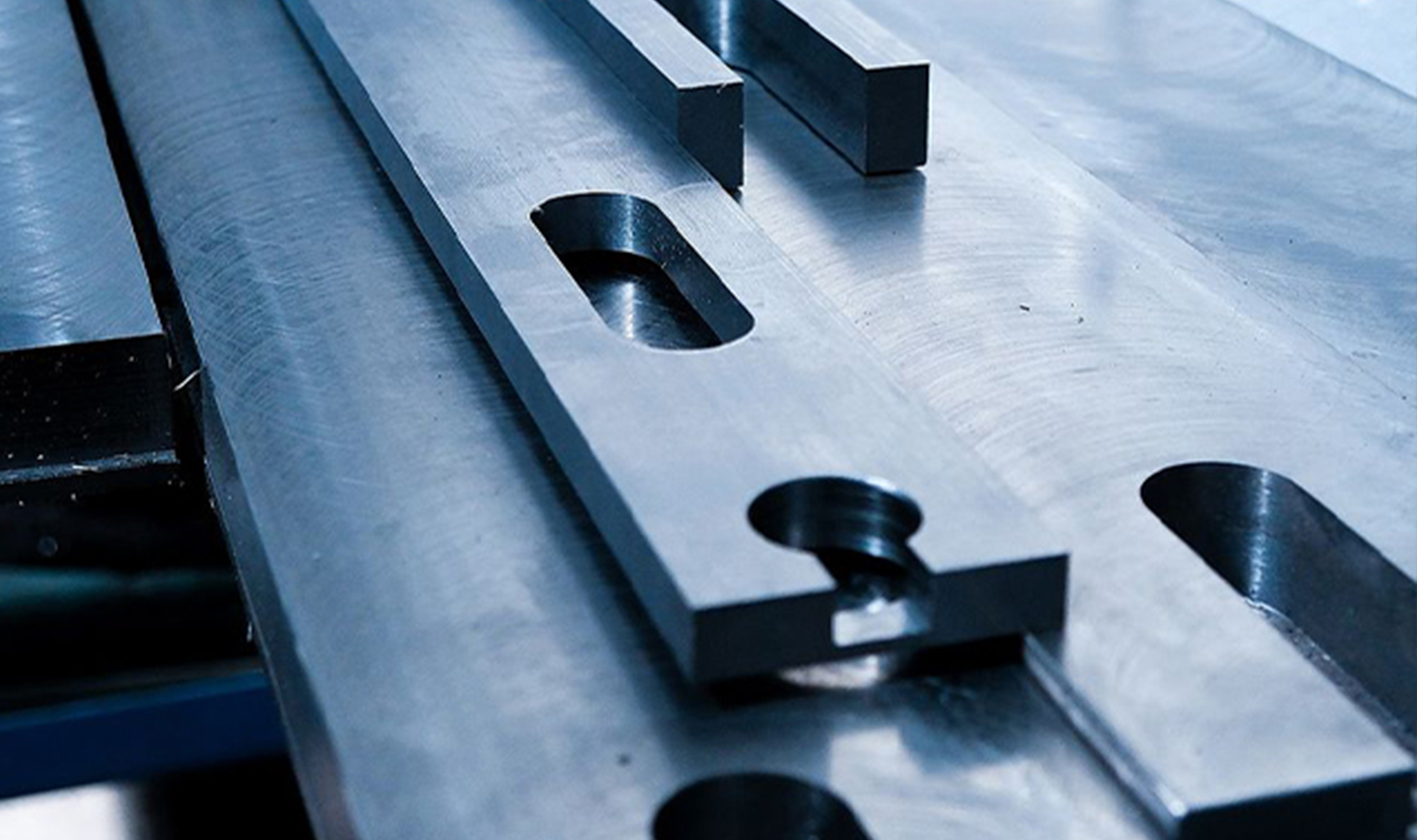
Understanding Crowning Systems in Press Brakes
In the world of metal forming, press brake machines are invaluable tools for achieving precise bends and shapes. However, two critical components play a crucial role in ensuring the accuracy, consistency, and quality of these operations: crowning systems and lower beams. In this article, we’ll explore the importance of these components, how they work, and the advantages they bring to modern metalworking processes.
Crowning systems are essential in overcoming a common challenge faced during bending: deflection. As press brakes apply force to a metal workpiece, natural deflection occurs in the machine frame and tooling, causing inconsistencies in the bend angle along the length of the workpiece. Crowning systems counteract this deflection, ensuring a uniform bend from one end to the other.
“Crowning systems counteract this deflection, ensuring a uniform bend from one end to the other.”
Types of Crowning Systems:
1- Manual Crowning: In manual systems, operators adjust the crown manually to compensate for deflection. This approach is economical but can require experience and a keen eye to get consistent results.
2- Automatic Crowning: Automatic systems use sensors and software to detect deflection and automatically adjust the crown. This system is ideal for high-precision applications, as it provides real-time adjustments, ensuring the most accurate and repeatable bends.
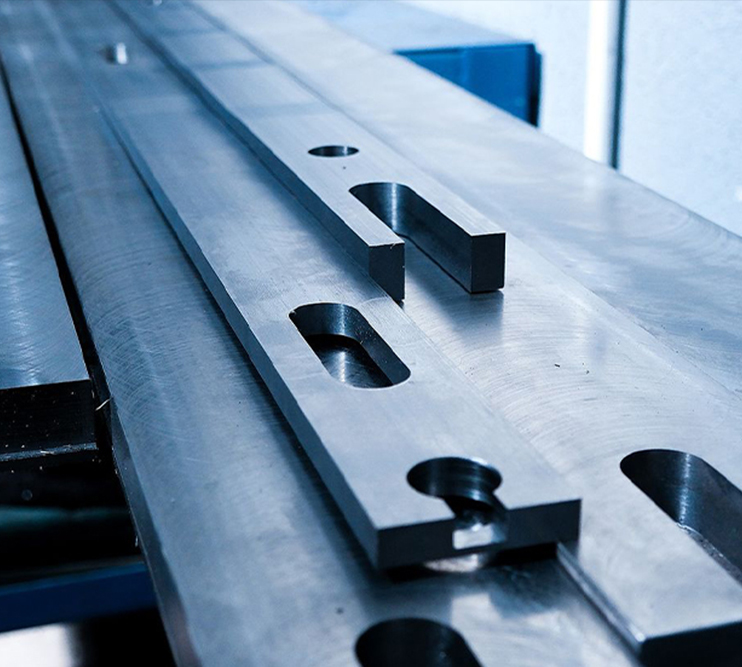
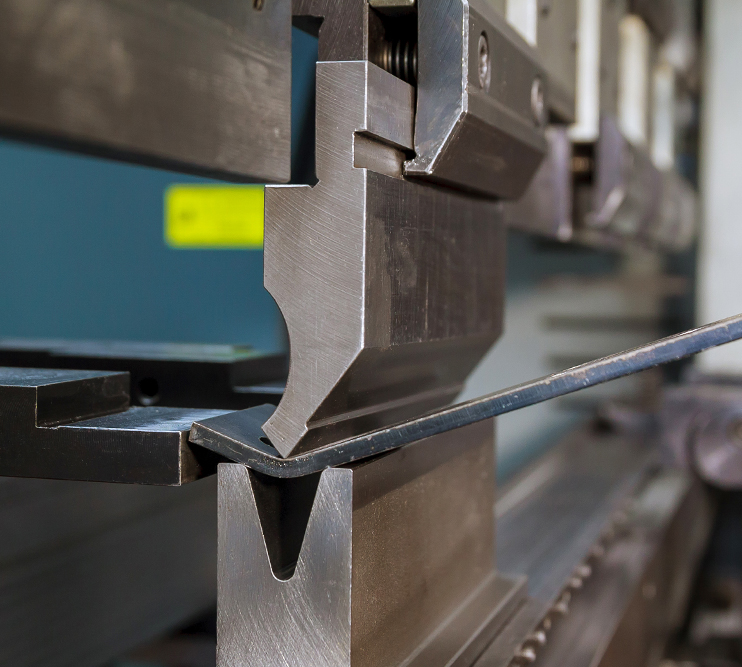
The synergy between crowning systems and lower beams is
what enables press brakes to achieve consistent, high-quality
results. While the lower beam provides stability and support,
the crowning system actively compensates for any deflection
that might occur during bending.